What types of heating / cooling technology is common for stainless steel tanks?
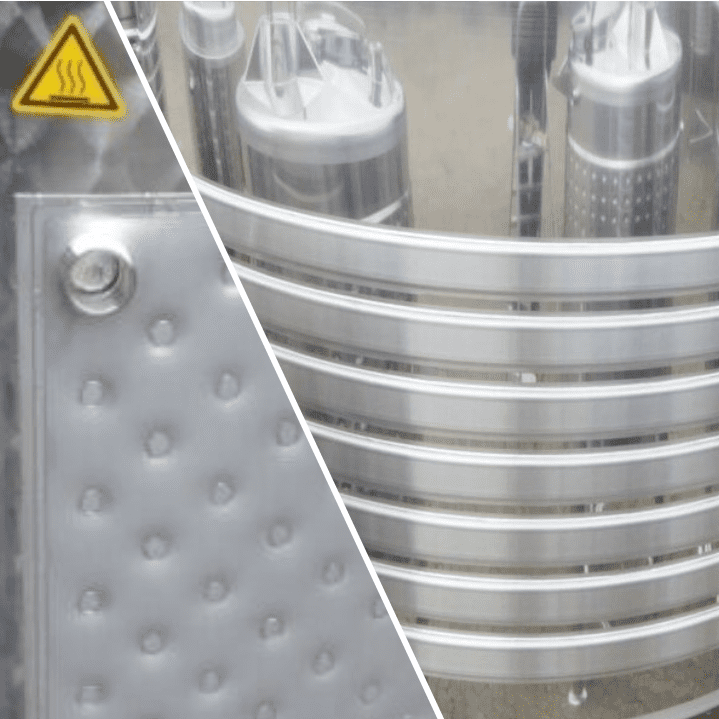
Many process engineering and production sequences require regular temperature control within the tank system. In some specific areas of application, such as a melting tank or reaction vessel, this functionality of heat exchange is the integral part of the process itself. However, there are various technical design characteristics that enable such temperature control.
We hence want to briefly present the most common technical designs of a heating / cooling circuit:
- Half-pipe coil
- Thermoplate / pillow-plate
- (Full) Pipe coil / heating coil
- Double jacket
- Immersion heater / tube bundle
- Electrical heating by means of trace heating / heating mat
- Electric heating (indirectly) through heat transfer fluid
Half-pipe coil
A half-pipe coil is characterized by an easily recognizable half-shell-shaped pipe segment, which is welded in tight turns around the outer wall of the tank or reactor. This type of temperature control is suitable for both liquid and vaporous media up to extremely high temperatures and pressure levels, depending on the exact design of the half-pipe coil (i.e. wall thickness, steel grade). Slightly modified variants include the rectangular half-pipe coil, which is flatter and more bevelled. The half-pipe coil is widely used in many demanding areas of application in the chemical and pharmaceutical industries. For example, for continuous temperature control with thermal oil, saturated steam or hot water.
Half-pipe coil of a brand-new Behälter KG stainless steel reactor
Thermoplate / pillow-plate
With this technology, a thin stainless steel sheet is welded onto the outer shell of the tank. The jacket space is then irreversibly inflated by high pressure and the thin Thermoplate sheet is thereby deformed into its classic, rounded, arched look. Depending on the design and material thickness, the thermoplate can be used with both liquids and steam. In contrast to the half-pipe coil, there are no unheated gaps between the heating zones with a Thermoplate jacket. Due to the resulting larger temperature exchange surface of the Thermoplate jacket, the heat transfer is superior. Another advantage of the Thermoplate compared to the half-pipe coil is a significantly lower amount of heating or cooling medium which is required. This is the result of the thin jacket space, compared to the half-pipe coils that often measure around 50-80 millimeters in diameter. Thermoplate (protected brand name) and pillow plate (technical term) are used colloquially as synonyms.
A slightly different design variation are so-called dimple plates. In this case, the wavy "dimpled" structure of the jacket is already pre-pressed before it is welded onto the outer shell of the vessel. This results in a slightly different look and lower pressure resistance, which is sufficient for temperature control with liquid media.
Thermoplate jacket of a Behälter KG tank, type "SDE-Flexmix"
(Full) Pipe coil / heating coil
The pipe coil looks similar to the half pipe coil, but the turns are designed as a full pipe. In order to ensure that the temperature is efficiently transferred to the medium in the tank, the full pipe coil is commonly installed inside the tank. This design is therefore a type of direct temperature control, since there is direct contact of the heating coil with the product inside the tank - in contrast to the half-pipe coil, which only comes into indirect contact with the medium through the outer shell of the tank. One advantage of the pipe coil is the relatively inexpensive installation as there is little welding work to be done on the tank itself. Full pipe coils are also extremely pressure-resistant due to their tubular geometry. The full pipe coil can also be easily retrofitted, exchanged or repaired in existing tanks. Disadvantages are dead spaces when cleaning the interior of the vessel, as well as the risk of cross-contamination of the storage medium with the heat transfer liquid, in the event of a leaking pipe coil.
Full pipe coil inside a tank for vegetable oils
Double jacket
The term double jacket is often used colloquially as an umbrella term for any form of temperature control or insulation of a tank and can therefore lead to misunderstandings. In the context of temperature control, the double jacket is to be understood as a second shell around the outer wall of the tank. This double jacket can only enclose the bottom of the tank or also the cylindrical part of the tank. For altering the temperature inside the tank, the double jacket is filled with heating / cooling medium (i.e. iced water, hot water). Due to the very large heat exchange area of the entire jacket space, temperature is transferred inside the tank. Disadvantages are the large demand for heat transfer liquid due to the large interior space of the jacket, as well as a generally lower pressure resistance, compared to other temperature control technologies. In the dairy industry, a pressureless double jacket is often used in combination with a trickle ring, through which the jacket space is sprinkled with ice water, thereby cooling the product space.
Example of a double jacket in the lower cylindrical area
Immersion heater / tube bundle
Often mounted horizontally in the cylindrical part of the tank, the immersion heater reaches far into the inside area of the tank and is in direct contact with the storage medium. The tube bundle itself can be heated by means of circulating thermal oil or hot water. Alternatively, there are also electric immersion heaters that can be heated directly by electricity. This type of temperature control can easlily be retrofitted into an existing tank with reasonable effort. A disadvantage of this technology is a more complicated cleaning process of the inside of the tank, due to dead spaces around the tube bundle.
Side-mounted tube bundle heating device in a melting vessel
Electrical heating by means of trace heating / heating mat
Electric heating can be implemented though trace heating cables, wired around the outside wall of the tank. In case of large outdoor storage tanks or tank containers, such trace heating technology is often used for frost protection or for relatively precise temperature maintenance.
This type of temperature control is also suitable for high-temperature applications, though an encompassing heating mat that can be installed around the outside wall of the tank. The heating mat already includes tightly arrange dtrace heating cables and serves itself as an insulation jacket. Such a heating mat can be individually adapted to all needs and can guarantee operating temperatures of over 300 ° C. Because of its very high energy consumption, such heating jackets are only advisable for small batch sizes (e.g. pilot plant reactors, transport containers, small melting vessels).
Silicone heating jacket of a Behälter KG tank, type "SDE-Flexmix"
Electric heating (indirectly) through heat transfer fluid
This type of temperature control features a double jacket (see description above) in which one or more electrical immersion heaters are incorporated. The double jacket, filled with thermal oil, is heated by though the immersion heaters and transfers this heat to the inside of the tank.
Are you looking for a heatable or coolable tank and still have questions that need to be clarified? Call us at any time or write to us at mail@behaelter-kg.de!
Sie möchten mehr zu dieser Leistung erfahren?
Sprechen Sie uns an.